液体阴极法电解
以含钙10%~15%的铜钙合金液体作阴极,石墨电极作阳极,电解氯化钙熔体制取富含钙的钙铜合金的过程。产出的钙铜合金经蒸馏获得金属钙。
使用铜钙合金作阴极,可在较低的电解温度(973K以下)下制得含钙65%的钙铜合金(含钙范围较宽)。钙铜合金中的钙用蒸馏法很容易与铜分离。蒸馏残余物即所谓贫合金,返回电解过程循环使用。由于钙铜合金含钙65%)的密度比电解质小,始终留在电僻槽底部,不会漂浮到电解质表面。
液体阴极法电解生产钙铜合金,可以采用单一氯化钙作电解质,但生产中广泛采用易熔和导电性好的由无水CaCl2 和KCl组成的混合电解质。随着电解的进行,电解质中的CaCl2 含量不断降低,需要定时往电解槽中补充新的无水CaCl2 ,以保持电解质水平。
液体阴极法电解生产钙的电流效率为72%,电能效率为30%,就是说有70%的电能消耗在电解槽的热损失和被废气带走的热损失的补偿上。电解时,金属钙从槽底析出,在电解液层下面形成钙铜合金,此时的电流效率随阴极和阳极电流密度的增加而提高。这是因为随着电流密度的增加,电流的无用消耗损失相对变小,即电流的利用率提高。但是随着电流密度的增加,电压也增大,电能消耗增加。极间距增大,电流效率也随之增加,因为极间距增大,钙与从阳极上析出的氯气发生的二次反应也会减弱。增大极间距和增大电流密度都会同样引起槽电压升高,*终导致电能消耗增大。因此,电流密度和极间距之间应保持一个*佳值。电流密度直接影响到电解析出的钙量。当电流密度过大,电解析出钙的速度超过钙向钙铜合金的扩散速度时,钙便会上浮到电解质液面并发生氧化燃烧,导致电流效率降低。在实际生产中,阳极电流密度一般控制在1.7~3.25A/cm2 。电解质中的水、NaCl、MgCl2 等杂质也会使电流效率降低。
液体阴极法生产钙采用矩形铸铁电解槽。为减少热损失,槽与外壳之间砌有绝缘的保温耐火砖。电解槽阳极由200mm×200mm×700mm的石墨块组成,阳极块用拉紧螺丝固定在金属横架上,电流通过软母线导向阳极,软母线则用压板固定在横架上,旋转电解槽侧部的手轮就可用于升降阳极。电解槽的上部盖有多块石棉水泥板。氯气由电解槽内经过电解槽端部的竖烟道导向电解下面的集气烟道,并从通风机抽出,经吸收塔处理后排入大气。电解槽的电流强度为10000~40000A,并有增大的趋势。钙电解生产一般由多台电解槽串联而成。
一个或几个以及一系列电解槽在安装或大修之后,需要重新启动。电解槽启动之前要用木柴烘烤2~3h,以除去水分。烘烤后彻底清除槽内灰渣,然后装入40~50kg预先经净化和干燥的电解铜或60~70kg贫合金。在电解槽底均匀地敷上一层铜块,调整阳极至阳极底面与铜层之间的距离不大于1cm。在电解槽壁和阳极之间的空间内填充200~250mm厚的由80%~85%CaCl2 和15%~20%KCl组成的物料,并注入50~60kg熔融电解质后,接通电源开始电解。当钙铜合金液面升至14~12cm时,合金富集过程结束。合金中钙含量在62%~65%时,便由槽内取出,但须保持有5cm深的电解液。富集的钙铜合金取出后送去蒸馏。
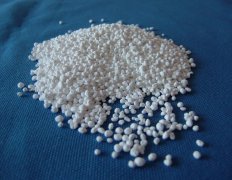